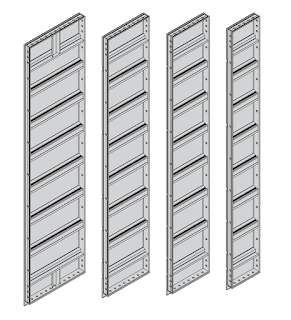
Wall Panel Aluminum Formwork: Best Practices for Optimal Results
Wall panel aluminum formwork has become a cornerstone of modern construction, offering unmatched precision, durability, and efficiency. It enables builders to create consistent, high-quality concrete walls with speed and cost-effectiveness. To maximize its benefits, following best practices for its design, assembly, usage, and maintenance is essential. This guide provides a detailed overview of these practices, accompanied by visual references.
What is Wall Panel Aluminum Formwork?
Wall panel aluminum formwork is a construction system that uses lightweight aluminum panels to form molds for pouring concrete. These molds are reusable, precise, and ideal for creating uniform concrete structures.
Key Advantages:
- Durability: Resistant to wear and tear, allowing up to 200-300 reuses.
- Efficiency: Reduces construction time significantly.
- Cost-Effectiveness: Minimizes the need for plastering due to smooth wall finishes.
- Sustainability: Recyclable and environmentally friendly.
1. Planning for Success
Thorough Design Analysis:
- Collaborate with formwork designers to customize panels for project-specific dimensions.
- Use advanced tools like CAD or BIM to visualize and optimize the formwork layout.
Material and Logistics Planning:
- Ensure timely delivery of panels and assembly tools.
- Allocate skilled labor for installation and dismantling.
2. Preparing the Worksite
A clean and organized worksite is critical for successful installation.
- Level the Base: Remove debris and ensure the foundation is even.
- Mark the Layout: Use laser levels and chalk lines for precise placement of panels.
Tip: Clean the panels to remove dust or oil residues before installation.
3. Proper Assembly Techniques
- Begin with Corners: Install corner panels first for structural stability.
- Secure Connections: Use pins and wedges to lock panels tightly.
- Align Accurately: Utilize alignment tools like string lines and spirit levels to ensure straight walls.
4. Concrete Pouring and Vibration
Proper handling of concrete ensures the durability and aesthetics of the finished walls.
- Controlled Pouring: Pour concrete steadily to prevent overflows.
- Vibration: Use mechanical vibrators to eliminate air pockets and achieve uniform density.
Tip: Monitor the concrete consistency to avoid segregation.
5. Safe Dismantling Practices
After curing, remove the panels carefully to avoid damaging the structure or the formwork.
- Start from the Top: Dismantle panels systematically from top to bottom.
- Inspect After Use: Check for any damage to the panels for timely repairs.
6. Maintenance and Storage
To extend the lifespan of aluminum formwork, maintain and store it properly:
- Cleaning: Use water and soft brushes to remove concrete residues.
- Repairing: Address dents or scratches immediately.
- Storage: Stack panels horizontally in a dry and secure area.
Pro Tip: Apply a protective coating during long-term storage to prevent corrosion.
Best Practices Summary
- Plan every detail of the project to minimize errors.
- Inspect panels for quality before installation.
- Ensure precise alignment during assembly.
- Handle concrete with care during pouring and curing.
- Dismantle and clean the panels properly to preserve their condition.
- Follow a regular maintenance schedule to maximize reuse cycles.
Conclusion
Wall panel aluminum formwork is a transformative technology for the construction industry. By adhering to these best practices, builders can enhance efficiency, reduce costs, and achieve superior concrete structures. Whether for residential or commercial projects, this system ensures long-term benefits when used correctly.
For additional guidance, consult with aluminum formwork manufacturers or training experts to tailor solutions to your specific construction needs.